چگونگی تولید کامپوزیت به روش RTM
یکی از روش های متداول تولید قطعات کامپوزیتی روش قالبگیری با انتقال رزین (RTM) است; روش RTM یک فرایند قالب بسته کم فشار است; که از طریق آن با به کارگیری پلیمرهای مایع گرماسخت تقویت شده با انواع گوناگون الیاف; قطعه ای با کیفیت سطح و دقت ابعادی بالا تولید می شود.
توضیحات کلی درباره روش RTM :
معمولاً در این فرآیند پلیمرهایی از خانواده اپوکسی، وینیل استر، متیل متاکریلات، پلی استر یا فنلیک; و تقویت کننده الیاف شیشه استفاده میشوند; سایر تقویت کننده ها از جمله الیاف کربن، آرامید یا الیاف سنتزی به تنهایی یا در ترکیب با یکدیگر برای کاربرد در شرایط دشوارتر به کار گرفته می شوند.
نوع زمینه پلیمری و تقویت کننده; عامل تعیین کننده جنس قالب و کارایی آن از نظر مکانیکی و سطحی است.
علاوه بر پلیمر و تقویت کننده، میتوان برای افزایش دیرسوزی، مدول خمشی و کیفیت سطح نهایی; از پرکننده های معدنی نیز استفاده کرد.
در این فرایند تقویت کننده ها به صورت پارچه بافته، الیاف سوزنی و… به شکل خشک درون قالب قرار داده می شوند; این الیاف یا قبلاً به شکل دقیق قالب تهیه می شوند (به صورت پیش شکل); یا در حین فرایند چیدن آنها در قالب، با دست شکل داده می شوند.
بعد از قرار دادن الیاف درون قالب; یک رزین که از پیش با کاتالیزور مخلوط شده است به درون قالب بسته تزریق شده و الیاف را در بر می گیرد; ممکن است روی سطح قالب پوشش ژلی اعمال شود; فرایندی که طی آن، قبل از قرار دادن الیاف درون قالب، روی سطح قالب پوشش داده می شود.
مزایا و معایب
برتری ذاتی روش RTM تزریق رزین با فشار کم است; فشار تزریق رزین در حین پر شدن قالب معمولاً از ۶۹۰ کیلوپاسکال تجاوز نمی کند.
دیگر برتری های این روش در مقایسه با فرایندهای قالب باز عبارتند از: کمتر بودن میزان انتشار گازها و بخارات ناشی از پلیمریزاسیون یا پخت رزین، شرایط کاری تمیزتر، پایداری ابعاد بیشتر قطعات تولیدی، کیفیت خوب هردو سطح قطعه تولیدی و فرایند تولید سریعتر.
با این حال باتوجه به هزینه بالای ساخت قالب و نیاز به گره های نگهدارنده قالب و تجهیزات کمکی; در مجموع روش RTM از نظر هزینه و حجم تولید فرایندی متوسط محسوب می شود; و در اصل بین دو دسته فرایندهای قالب باز کم هزینه با تولید کم و فرایندهای پرهزینه قالبگیری با پرس با تولید انبوه قرار دارد.
همیشه این سؤال مطرح بوده است که آیا روش RTM در مقیاس وسیع در صنعت کامپوزیت مورد استفاده قرار گرفته است؟
صنعتگران زیادی در سالهای گذشته روش RTM را به عنوان روش تولید قطعات کامپوزیتی آزمایش کرده و به کار گرفته اند، اما تنها تعداد کمی از آنها برای مدت زیادی از این روش استفاده کردند و تقریباً میتوان گفت هیچ کدام از آنها روش RTM را به عنوان روش انحصاری تولید خود نپذیرفتند.
فرایندی که امروزه تحت عنوان RTM مورد استفاده قرار می گیرد در واقع RTM سبک (Light) یاLRTM است. اگرچه ممکن است این فرایند نتواند همانند RTM سنتی فرایندی با حجم تولید متوسط (۱۰۰۰ تا ۱۰۰۰۰ قطعه در سال) به حساب اید اما نسبت به فرایندهای قالب باز از سرعت بالاتری برخوردار بوده و برتری های واقعی یک فرایند قالب بسته را به همراه دارد. باتوجه به برطرف شدن معایب روش RTM در LRTM، اعتماد تولیدکنندگان به این روش روز به روز بیشتر می شود، به طوری که امروزه آمارهای موجود از به کارگیری گسترده این فرایند توسط صنعتگران حکایت دارد.
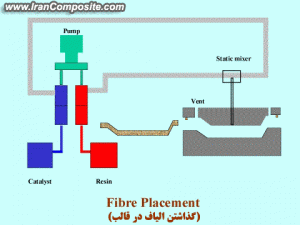
قالب
مهم ترین جزء فرایند LRTM، قالب است. در فرایندهای قالب بسته، قالب دارای دو نیمه است; یک نیمه قالب نسبتاً صلب و نیمه دیگر نسبتاً انعطاف پذیر است; در واقع یک نیمه قالب سفت تر از نیمه دیگر آن است.
معمولاً نیمه صلب قالب با استفاده از فناوری و موادی ساخته میشود که برای ساخت قالب های فرایند قالب باز به کار گرفته می شود.
تنها تفاوت مهم قالب فرایندهای قالب باز و نیمه صلب قالب فرایند LRTM; این است که عرض فلانج دور قالب در LRTM حدود ۲۵-۱۵ سانتی متر است.
قالب فرایندهای قالب باز با فلانج دارای سیستم پاشش; بدون هیچ گونه تغییری میتواند برای قالبگیری IRTM استفاده شوند. بعضی اوقات قالبگیر میتواند برای شروع، یک فلانج به قالب موجود اضافه کند; ولی برای قطعات کوچکتر معمولاً ساخت قالب جدید ساده تر است; ذکر این نکته ضروری است که چرخه های قالبگیری سریع، نیازمند قالب هایی با کنترل دما هستند که عملاً فرایند ساخت متفاوتی با قالب های باز دارند.
معمولاً در فرایند LRTM، نیمه صلب قالب; نیمه ماده قالب و دارای محفظه خالی و برعکس نیمه انعطاف پذیر قالب، نیمه نر و دارای برجستگی است.
نیمه انعطاف پذیر معمولاً یک کامپوزیت چند لایه است که با روش لایه چینی دستی از رزین های وینیل استر و الیاف کوتاه تولید می شود; استفاده از قالب های شفاف از این جهت سودمند است که به قالبگیر اجازه مشاهده جریان رزین در داخل محفظه قالب را می دهد; البته این مسأله برای قالبگیران ماهر و باتجربه از اهمیت کمتری برخوردار است.
نیمه انعطاف پذیر قالب معمولاً روی نیمه صلب قالب ساخته میشود و برای ایجاد فضای خالی بین دو نیمه; از ورقهای موم استفاده می شود (البته روشهای سودمند دیگری نیز وجود دارد که دارای نتایج مطلوبی هستند); فلانج نیمه بالای قالب بایستی با فلانج نیمه پایینی هماهنگ باشد.
همچنین نیمه بالایی قالب باید دارای اجزای مشخصی باشد که نقشی کلیدی در پیشرفت و موفقیت فرایند دارند; این اجزا عبارتند از واشرهای داخلی و خارجی فلانج برای آب بندی در ایجاد خلاء; روزنه یا روزنه های تزریق و دست کم دو روزنه خلاء که معمولاً یکی از آنها در نزدیکی مرکز قطعه تعبیه می شود.
از این روزنه همچنین برای تزریق مایع جداکننده استفاده می شود. علاوه بر قالب; پمپ تزریق رزین و پمپ خلاء ازجمله تجهیزات ضروری این فرایند به شمار می آیند; سیستم خلاء میتواند شامل دو پمپ ونتوری ساده ۲۰ دلاری و یا دارای تجهیزات ۱۰،۰۰۰ دلاری باشد; برای پمپ رزین اغلب قالبگیران از هرآنچه در دسترس است یا با آن آشنایی دارند استفاده می کنند; نمونه هایی از پمپ های مورد استفاده عبارتند از پمپ دنده ای، پمپ دیافراگمی، پمپ دودی و…
فرآیند
در این فرایند قطعات میتوانند بدون پوشش ژلی یا با پوشش ژلی بر روی یک یا هردو سطح تولید شوند; آماده سازی قالب و اعمال پوشش ژلی همانند فرایند قالبگیری باز است. هنگام اعمال پوشش ژلی، فلانج های قالب توسط کاغذ یا ماسک های قابل استفاده مجدد پوشانده می شوند.
به طور ایده آل هنگامی که پوشش ژلی هنوز چسبناک است; تقویت کننده ها در محفظه مادگی قالب قرار می گیرند; پوشش چسبناک ژلی کمک می کند که تقویت کننده ها هنگام بسته شدن قالب در جای خود ثابت باشند.
انواع مختلف تقویت کننده ها و الیاف میتوانند مورداستفاده قرار گیرند; ولی استفاده از مواد ویژه باعث تسهیل فرایند و افزایش سرعت آن میشود.
سایر تقویت کننده ها و انواع مغزی ها میتوانند به همراه مت های شکل پذیر به کار گرفته شوند تا نتایج مطلوب به دست آید.
پس از آنکه همه مغزی ها و تقویت کننده ها در جای مناسب خود قرار داده شدند; قالب بسته می شود. این عمل با قراردادن نیمه بالایی قالب روی نیمه صلب قالب با دست انجام می شود; معمولاً نیروی جاذبه همراه با لرزش های کوچک، فشار کافی را جهت بسته شدن قالب و آب بندی آن توسط واشر محیطی فلانج ایجاد می کند.
در این لحظه خلاء کاملی در فضای بین واشرهای داخلی و خارجی فلانج اعمال می شود; این خلاء باعث ایجاد فشاری معادل چندین تن حتی روی قالبهای کوچک میشود.
هنگامی که دو نیمه قالب به طور کامل فشرده شدند; از طریق روزنه مرکزی نیمه بالایی قالب یک خلاء نسبی اعمال میشود; در این هنگام قالب آماده دریافت رزین است.
رزین از نقطه ای خارج از لبه قطعه و درون واشر داخلی وارد می شود; هنگامی که تقویت کننده ها در قالب قرار داده می شوند; یک فضای خالی بین الیاف و واشر درونی باقی می ماند که این فضا محلی برای جریان رزین است. در نتیجه قبل از آنکه رزین به داخل تقویت کننده ها نفوذ کند دور تا دور آن را در قالب فرا می گیرد. برای قطعاتی که طول آنها بیش از ۱۲۰ سانتی متر است معمولاض بیش از یک روزنه تزریق به کار گرفته می شود.
با آغاز جریان رزین درون تقویت کننده; رزین به سمت روزنه خلاء که در مرکز قطعه قرار گرفته است پیش می رود; پس از آنکه قالب به طور کامل پر شد پمپ تزریق خاموش شده و لوله تزریق جدا می شود.
هردوی خلاء های کامل و نسبی باید تا زمانی وجود داشته باشند که قطعه به قدر کافی پخت شده و بتواند از قالب جدا شود.
هنگام جدایش قالب; از طریق روزنه مرکزی اعمال خلاء; فشار ملایم هوا اعمال می شود تا عمل جدایش قالب تسهیل شود; ذکر این نکته ضروری است که در روش RTM سنتی تزریق تا زمانی که مشاهده شود قالب پر شده است ادامه می یابد; ولی در روش LRTM میزان رزین موردنیاز پیش بینی شده و قالب تا آن زمان پر می شود.
بنابراین قطعه ای با دقت و کیفیت بالا تولید شده و از بیرون ریختن رزین اضافی جلوگیری میشود.